Increasing cases of wall tie failure, causing collapse of a house.
Wall tie corrosion, causing collapse, was quite a rare occurrence as I started my journey (back in the early 90’s when I joined Brick-Tie). But over the past decade or two the problem has grown more common.
Some say it’s due to increasing severity and frequency of storms. Those with higher wind speeds. Fair comment, gales these days seem more powerful than in the past, and the media are always warning about ‘Cyril’, ‘Claud’, ‘Amy’ or the next charmingly named super-gale.
I have my doubts though, this is not the only reason, or even main one. The truth is that corrosion of structurally important cavity wall ties has been known about since the mid 1980’s. That’s about the time the first few corrosion induced wall collapses happened in Yorkshire.
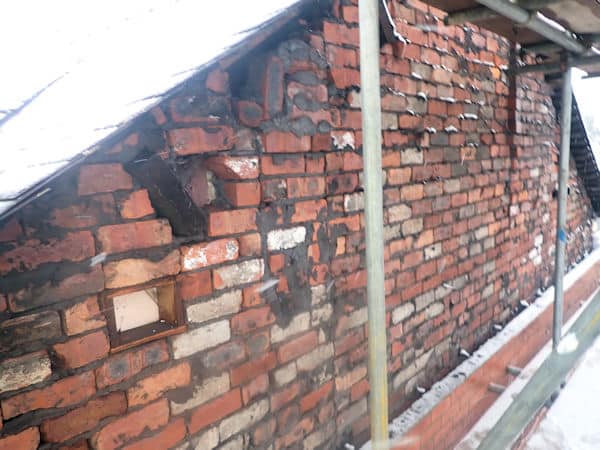
The real cause of collapse is not the wind – it’s hidden wall tie corrosion.
Fast-forward nearly 30 years and as a firm, Brick-Tie expect to deal with a several such events every year. And over the North of England the increase is at least ten-fold over the past.
Climate change can be debated, but there’s no doubt that once metal starts to rust it slowly weakens, and changes, eventually losing all its strength. It may take years or decades, but time does its work. Many of the collapses I see are houses built in the early 20th century. I see modern collapses too, but they are often due to poor workmanship, or lack of lateral restraint straps – rusting ties, leading to collapse is rarely an issue in houses built after the 1980’s.
In the most recent case the gable of a house in Leeds collapsed during a windy day without warning, dropping the entire apex area of dense brick onto the garden. If anyone had been in the garden on the path alongside the house they would have been killed or severely injured. Our clients insurers and structural engineer called Brick-Tie in.
The cause? Well it was windy, but many days are. A close inspection revealed the truth of it. The old wall ties, installed as the house was built, before world war 2, had just rusted away. As shown in my images the metal which connected the gable wall to the house was still intact. However, the section hidden from view, built in to the outer leaf, was totally corroded. A quick glance down the cavity at one corner shows ties that whilst looking rusty, seemed sound.
A specialist approach to wall tie corrosion
But close inspection showed they had snapped right at the joint with the external wall. So when the wall collapsed, that stronger section of wall tie crossing the cavity, was left projecting ineffectively in the open. They looked like rusty teeth. It’s a fact that wall ties are only as strong as the weakest section, that is where they fail. I have never seen a wall tie snap in the middle of the cavity – it’s always at the inner face of the outer skin of brick, or within the outer leaf. So only a close and thorough inspection by an experienced specialist can tell anyone what condition their wall ties are in.
They’d probably been in this condition for years, the wall waiting for just the right direction and strength of wind, to finally break the bond, and allow the slender panel of brickwork to fall out. I’ve had many-a-builder point to ties in similar condition and tell me “They are miles stronger than modern ties – look at the thickness of that, it’s just surface rust”, only for me to expose just a little bit more and reveal the awful truth.
The huge pile of brickwork on the garden stood witness to the high strength of the masonry, parts of the collapsed section impacted the lawn without losing form – the bricks still bonded together by the rock-hard mortar. Yes, well built, but the wall was doomed the moment it was tied with bitumen painted mild steel ties, bonded in corrosive black-ash mortar.
The thing is, people imagine that old buildings are somehow better or stronger than new. This has a little truth in it, the materials were hard and heavy. But all that means is the wall was heavy and solid enough to withstand the wind for years. Years during which it was self-supported by gravity only. Held vertical by wall ties eaten away by rust. All that the heavy masonry added was a few year’s grace. Failure was inevitable. The wind tipping it just a little out of plumb was enough for gravity to turn from friend to enemy, and it fell over with a bang.
Brick-Tie – fighting the effects of wall tie corrosion for 38 years!
We can expect many more of these collapses in future. However, due to the diligence of building surveyors and structural engineers, very many homes now have effective remedial wall tie systems installed. The improvements are virtually invisible, but I take some pride in the knowledge that Brick-Tie have certainly saved many homes from a similar fate. We’ve installed millions of ties in tens of thousands of buildings across the north. These stainless steel ties are tested during installation, to a tensile force beyond any they will be subjected to by the strongest of hurricanes – guaranteed.
It makes sense to have one of our specialist surveyors check the condition of any older property’s wall ties. Our experts have the experience, equipment and skill to locate and inspect all wall tie types. If work is required the quotation is a fixed price quotation, we have never issued wooly estimate, so beloved of some builders, and not a few wall tie firms who we won’t name. We don’t ask for deposits before we fix your wall ties. That’s because our clients trust us to fix their homes, and we in turn trust them to pay us, for a job well done. As Helifix approved installers we are trained and sanctioned to installer the best remedial systems. Our 25 year guarantee is cast iron – many have expired now, having done their job, we’ve been going so long!
As Yorkshire’s most experienced and highest quality firm, owned by an employee trust, you can be assured that everyone you deal with will be friendly, honest, efficient, and competent.
For advice, surveys, or quotations, contact us now.