What is wall tie survey? What are wall ties anyway? Well, in answer to what are wall ties, it’s best to read the dedicated post on our MD’s blog which answers this here (what are wall ties?).
This post is about the practical aspects of the wall tie survey itself. What happens and what the report is likely to contain.
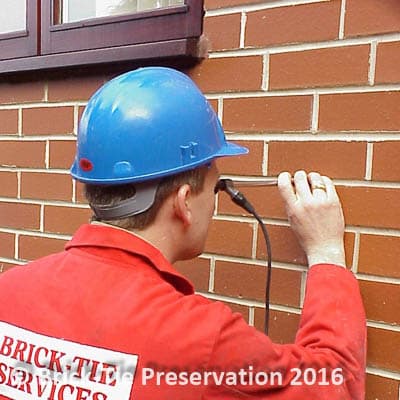
The need for a cavity wall tie survey can arise for several reasons:
A house may be quite old and metal ties in older houses can sometimes rust and fail, so the survey may be just a precaution, to check that wall tie corrosion isn’t an issue
Wall tie corrosion may be suspected, because of cracking in the wall, perhaps noticed by an owner, but more often than not, a matter raised by a surveyor, acting for a home buyer or a mortgage lender.
There may be a bulge or other defect which suggests a problem and the wall ties need checking as a process of illumination, so that the cause of the movement can be found.
Whatever the reason for the wall tie survey, the procedure is straightforward and usually takes less than an hour or so.
So what will the Wall Tie Surveyor Do?
After arrival on site and a brief introduction and reassuring chat with the owner, the surveyor (with the owner’s permission), will carry out an external appraisal of the house; Its constriction details; whether there is a cavity at all; is there cavity wall insulation present; are there any cracks and if so what size and shape etc.
Having done this he’ll then use a metal detector to locate the positions of the wall ties. This is usually done at ground level, but sometimes he may need to use a ladder, particularly if there are cracks at higher level or if the house has different materials in the walls, such as naked brick at ground level and rendered brick or stone at higher level.
Having found some ties to inspect a re-chargeable drill is used to form an inspection hole near each one; usually about 12mm in diameter and formed in the bed-joint (between the bricks or stones, if these are not covered by render or pebble-dash).
To inspect the ties, a boroscope is used. This is a robust version of the endoscope, which is basically a type of periscope within a 10mm diameter steel tube, with a viewing window for looking at the ties in the cavity and a light source to illuminate the target wall tie. Where the cavity is not insulated a remarkably clear view of the wall ties is possible. Homeowners and clients are more than welcome to ‘shadow’ our surveyor and even look at the wall ties themselves.
The wall tie inspection used to be quite a subjective process with one surveyor’s “failing” tie, judged as “okay” by another surveyor. This led to disagreements and confusion. Thankfully in 1995 The Building Research Establishment (BRE), issued guidance in the form of BRE digest 401 “Installing Wall Ties “, which set out how to visually grade existing wall ties and what to recommend (or not), depending on the condition of them.
BRE 401 sets out nine classes of wall tie corrosion, ranging from number 1: Bright and shiny – no problem, though to number 9: very rusty and laminating – urgent repair required. Initially, the visual condition of the wall ties is used to decide on what action (if any), is needed.
However, the surveyor will also need to consider some other factors before a final decision is made:
Are there any cracks or movement caused by the distress of rusting ties?
What type of wall ties are present? Thick fishtail type of thin wire type wall ties?
Were there enough wall ties installed when the house was built and are they in the correct positions?
Is there cavity wall insulation present or is installation planned soon?
What is the wind exposure and orientation of the building?
Usually a decision can be made immediately, however our surveyor will then take photographs of the wall ties through his boroscope, for further inspection later and to keep a record of the findings.
The above procedure is the most usual approach, however sometimes the wall ties may be difficult to see. Cavity wall insulation can obscure the view through the boroscope, making imaging and viewing impossible. Rubble, other debris or an unusually narrow cavity can also frustrate a boroscope wall tie survey. In these cases a more invasive method is needed.
This is how…
The wall ties have been found with the metal detector and now a small hole or two are formed in the bed-joint, exactly at the tie location. A chisel is then used to widen the gap so that eventually the wall tie is visible in the bed-joint, cleared of debris and available for inspection and imaging. This takes a little longer than a standard boroscope survey. The disturbed bed-joint is made good, however, in cases where a wall is rendered or pebble-dashed, there will be an unavoidable ‘patch’ of repaired render, which will not match the original material.
On completion and usually the same day, our surveyor will write his wall tie report.
The Wall Tie Corrosion Report contains all the essential information you need including:
The construction of the wall.
What type of existing cavity wall ties are present and whether they are galvanised, pitch coated or stainless steel?
What condition they are in, using BRE 401 as a guide.
Some images of the ties taken through the boroscope, annotated for location and images of the ties exposed in the bed joints, if that method was necessary.
In cases where the ties do not require any remedial work that’s it – job done.
However, if the condition of the ties falls foul of BRE 401 or, if there are factors which require acceleration of the timescale for wall tie replacement (impending cavity wall insulation for example), a wall tie replacement specification and a quotation will be issued as part of your wall tie report.
This will include the reasons for the recommendations, a detailed specification on what is needed and included in the quotation for the wall tie replacement; essential safety information, which is a legal requirement as the wall tie installation involves scaffolding and construction work, and of course the quotation itself, which is always a fixed price and never an estimate.
The wall tie report is designed to comply with BRE 401 so it also includes details on the qualifications of the staff who will install the new remedial wall tie system; their experience; the testing procedures for the new wall ties and the nature of the wall tie guarantee and the insurance in place to protect the guarantee for its entire duration.
There are exceptions to the above, because not all houses fit a standard ‘model’ and the surveyor may need to modify his approach to reach a sensible and credible decision.
Following this, the surveyor will make-good the inspection holes and sweep up any dust before leaving site.